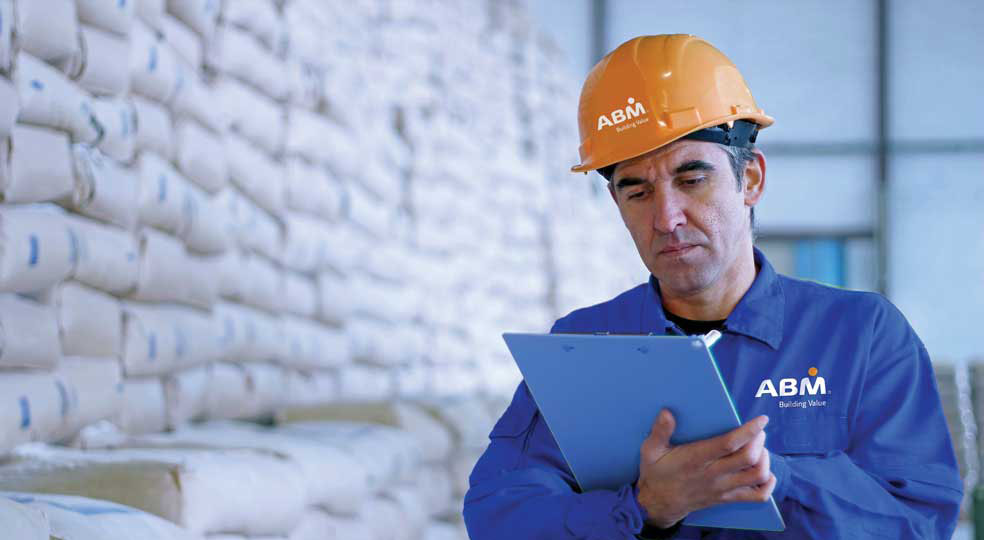
How Teamwork Drives Quality
The Schwan Food Company
“Employees take pride in their jobs.” • “We’re all part of the same team.” • “There’s no difference between Schwan’s people and ABM’s people.”
If you talk to the management at Schwan Food Company’s 200,000 square foot facility in Suwanee, Georgia, you’ll hear comments such as these over and over. The operation’s success is attributed to the high quality employees—their training and their attitude. Not surprisingly, the facility experiences low employee turnover because of the mutual respect all around. The culture of trust, equality, and teamwork begins with top management and permeates throughout.
The main activities at this site relate to the shipping and receiving of frozen food products. About 60 percent of the staff are ABM employees (product selectors, truck stackers, forklift drivers, janitors, and a project manager).Even though they handle millions of cases of food per year, their safety record is nearly perfect. And, their damage rate is a mere one percent—the lowest of all Schwan Food Company’s similar operations.
It Begins With Recruiting
ABM Project Manager (PM) Oscar Suarez know show to spot people with the right attitude. When he’s interviewing, he encourages applicants to talk about themselves—their experience; why they left their last job; what expectations they have; what are their hobbies, pets, interests, etc. To a great extent, Oscar bases his decision on good character—honesty and sincerity—and his own affinity with the applicant. Likewise, the right applicant recognizes the sincerity of the PM and can sense that Schwan is a good place to work.
Part of the Team from Day One
Oscar introduces new team members to the others, one-on-one or in groups, at break time. He has an open-door policy, and people know they can come to him with any questions or concerns. His office is near the loading dock, and all managers are visible and accessible. Schwan’s General Manager, Jeff Cole, is no exception. He’s been described as an extraordinary people-person who treats everyone as an equal. Recently, when an ABM forklift operator’s wife had a premature baby, Cole visited them in the hospital. Because he travels a lot, he likes to occasionally hold roundtable discussions. These consist of five employees meeting with him voluntarily to discuss issues and ideas. Once, an ABM employee invented a tool to make wrapping plastic around pallets easier, and that tool is still used.
Safety is an Ongoing Process
Being well versed in safety is important for people who work around freezing temperatures and forklifts. In addition to ABM’s annual safety program and monthly training sessions, the employees get updates and reminders via a daily safety topic presented in the break room. The PM keeps it simple, stressing the important data, giving real world examples that people can relate to, and allowing hands-on demonstrations when possible. If training involves a fire extinguisher, for example, he asks each person to hold it and examine it, so its weight and features are familiar to them. Any time the PM sees confusion in their eyes, he continues explaining until he can see, “I got it” on each face. The training pays off at inspection time: In April 2017, the operation received a985 out of 1000 in an American Institute of Baking (AIB) safety inspection.