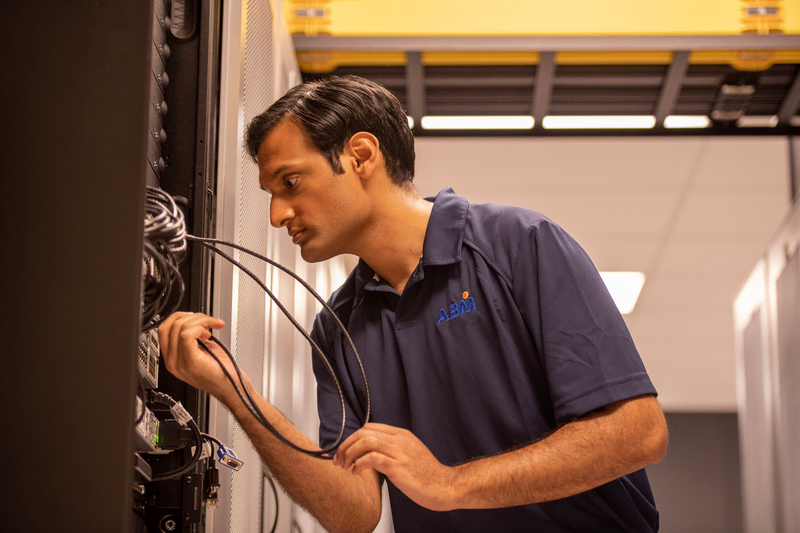
Keeping New Data Center Electrical Testing On the Rails
New data centers of every size now face performance demands up to “five nines” (99.999% uptime) – now from day one. Confidently meeting that mark puts electrical acceptance testing for new data center construction above the status of safety net or insurance policy. Efficient testing is now crucial to flipping that on switch on time – and it staying on.
Six Months to Day One
Shrinking construction periods for data centers are piling pressure on every process, and testing and commissioning are no exceptions. Since acceptance testing is key to identifying issues that production pressures can exacerbate, the value of testing only rises with time pressures. Planning for the practicalities of efficient, safe testing ensures that schedules are kept, including the overall data management needed to deliver organized results on time.
Data or It Didn’t Happen
If a testing schedule is completed,
the parameters correctly set and the processes verified, but those results aren’t available, then the work really isn’t done. Attention to rigorous data management ensures that acceptance and reliability data is collected and documented properly, in a timely way. Productive data management practices include:
- Dedicated, on-site data coordination
- Electronic information capture
- Planning for proprietary systems
A compressed testing schedule can result in multiple testers working long hours, generating a lot of data in a short amount of time. Resources need to be dedicated to capturing that data and ensuring that its available in an organized way. An on-site data administrator increases efficiency for the testing team and ensures data isn’t misplaced or misinterpreted. A dedicated data administrator also increases efficiency and timeliness by serving as a focal point for communications and a reservoir for the expertise needed to prepare data for proprietary systems.
Tools to enhance data management increase speed and bandwidth for testing. The ability to test in the field should be supported with on-site tools to electronically capture information. Taking the paper out of paperwork cuts down on transmission and data entry errors and speeds synchronization with proprietary systems. Knowledge of the data systems demanded by all parties is key. Organizing the testing data to fit the system of each stakeholder – and each reporting and compliance requirement – is a prime need that demands unique expertise. Electrical testing partners should also be able to provide alternatives to proprietary systems if the contractor has a need.
Planning a Partnership to Relieve Time Pressure
Data management is a good example of a place where the prime contractor, the commissioning agent, and the electrical testing team need to be aligned. Communication needed for that alignment can take time away from the prime contractor: more information to capture, more to reiterate, more to verify. A forward-thinking testing team steps up to the responsibility of communications alongside the contractor, as a partner. By reducing the need to repeat and transfer knowledge and needs, contractors gain back time, and testing providers can react faster and more flexibly to requirements and changes.
Changes will happen, even with the best of the plans in place. Acceptance and reliability testing that happens at pace also needs to be flexible, and the testing company should be able and willing to take ownership of that flexibility, so it doesn’t negatively impact the schedule – or the budget. One key factor to plan for is scalability. If more resources are needed, commissioning companies should be able to scale testing, data management and reporting efforts to protect the schedule.
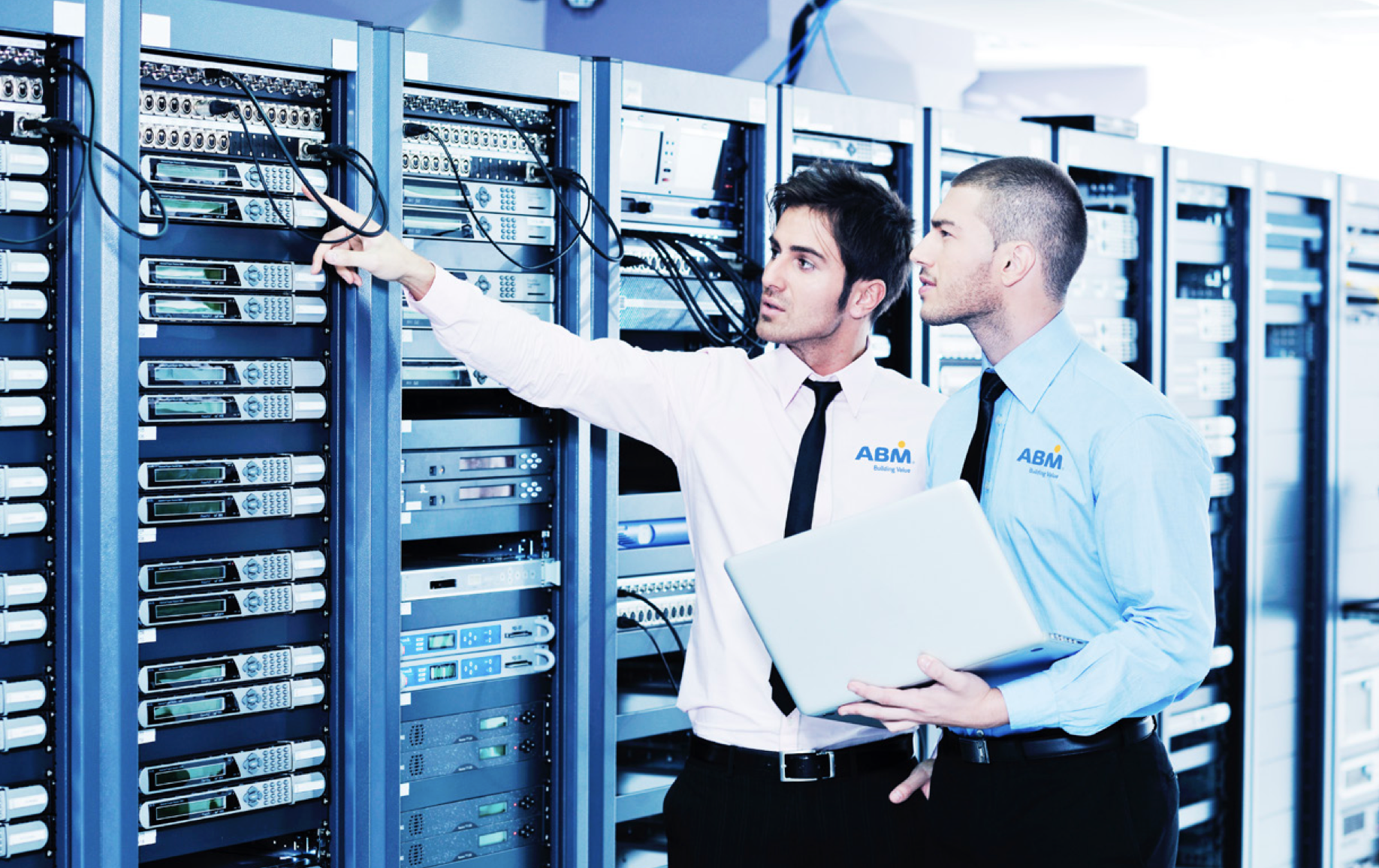
The cost of scalability is also a factor. Testing companies should take into account a reasonable assessment of the time that technicians and teams will need. The capacity to meet changing needs protects the schedule. A testing client of ABM faced this lack of scalability on a new Raleigh data center construction. Another testing company assigned certain cable terminations could not expand to meet the timeline. The ABM acceptance testing team on site had the capacity to take on the additional cable terminations within the client’s timeline, and the schedule was
met. Cost estimates that rely on assumptions that no overtime will be needed, or that changes will be minimal, are a warning that flexibility and scalability aren’t at the forefront of the tester’s plans.
Testing at the Speed of Safety
Testing power distribution assets and systems can be done safely and at pace. A testing company with extensive data center experience will have their own in-house safety policies and procedures that meet or exceed OSHA and NFPA standards while preserving an efficient schedule, but they should also have the ability conform to site-specific or client-specific safety requirements.
Testing companies should have a culture of safety you can trust. One key signal of safety culture is NETA certification. Rigorous training required for certification of the company and their technicians includes safety training. The third-party requirement of NETA certification also ensures independent, fact- based results that identify problems immediately, so they can be addressed in a timely fashion.
What Good Data Does Going Forward
While the statistics for downtime causes currently put human error at 22%, the rest of the categories, including UPS failure and other issues, make it apparent that human error on a higher level is responsible for much more. Testing should be addressing issues that arise during construction,
but great testing partners also execute the hand-off properly. Clear, accessible data and documented processes give operators and maintenance teams responsible for the data center the tools they require to protect uptime going forward.