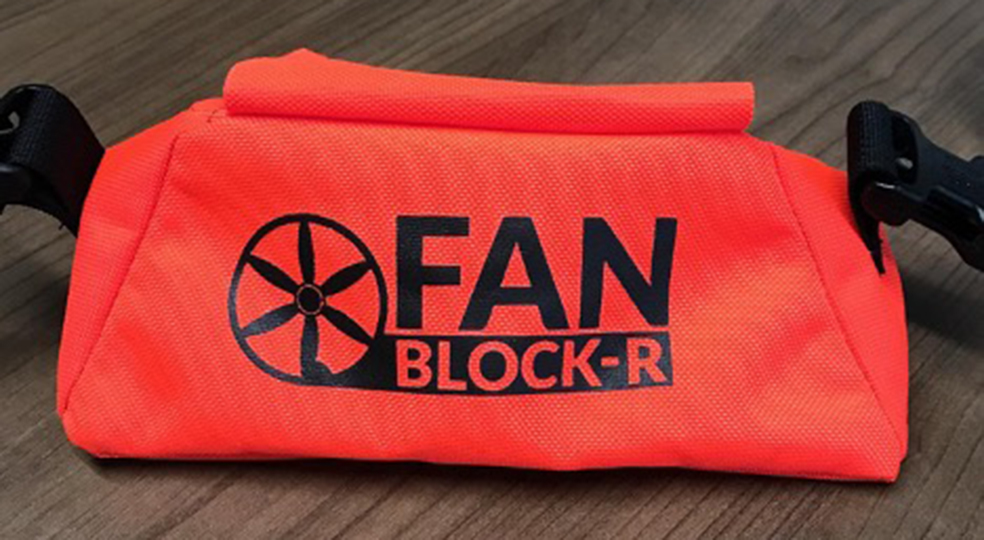
Safety Spotlight: How ABM’s Safety Director Prevents Injuries Through Problem Solving
To prevent injuries, organizations need to move beyond simply checking off items on their safety compliance checklist. Putting safety first means solving the problems that lead to accidents. That’s what ABM’sSafety Director, Tod Truettner, does every day. With nearly 30 years of experience as a safety professional, Truettner’s philosophy is to “Identify a problem and fix it.Find something that already exists or build something to engineer a hazard away.”
With the support of ABM leadership, Truettner is able to bring his problem-solving ideas to life. Here’s how one of his innovations, the Fan Block-R, is keeping workers safe every day.
Identifying the Problem
The Fan Block-R prevents fan blades and components from moving during service and maintenance. When servicing a fan, lockout/tag out procedures require that workers de-energize the fan by disconnecting it from its power source. But removing the electricity alone isn’t enough. The inertia generated by powering the fan down, as well as air flowing through the fan’s housing, can cause the blades to rotate, which is known as windmilling. The standard practice for solving this issue is to place a 2x4piece of wood in between the blades.
This rudimentary approach is widely accepted, despite its limitations. The 2x4 doesn’t prevent the belt or pulley from moving, and it doesn’t always hold against movement of the blades. When Truettner was asked what could be done to reduce windmilling, he realized there was nothing on the market that was more effective than the antiquated 2x4 method.
When the 2x4 method failed, it caused fractures, cuts, and even amputations. These injuries drastically reduce an employee’s quality of life, and may prevent them from being able to work again. For the company, they lead to lost productivity, high medical and retraining costs, fines, and reputational damage.
Engineering the Hazard Away
Truettner knew there was a better way to prevent unwanted motion when servicing fans, and that’s how the Fan Block-R was born. “Instead of telling them to shove a 2x4 into the fan, we went to that next level and built a product that’s only made for us,” he says.
With the support of his direct manager, he set about creating a tool that could be used to prevent windmilling. It needed to be durable, portable, and easy for engineers to incorporate into their existing practices. He worked with70E Solutions, a family-owned safety equipment supplier, to create a custom solution.
The Fan Block-R is an angled sandbag that can be used in multiple ways to prevent unwanted movement in fans and fan elements. Truettner calibrated the weight so that it can be placed on a fan’s blade to stop it from moving: “It weighs the exact weight needed to stop a 60-inch blade fan with a five mile-per-hour backdraft. Just the weight alone will stop it so you can just sit it in the path of the fan if you need to.”
The angles of the Fan Block-R are designed specifically to go in between a shiv and a belt. The sand filling makes it malleable enough to fit between the fan elements, and it has a strap to lock it in place. It can also be strapped to the back of the fan unit to lock the pulley in place.
Aside from the mechanics of the Fan Block-R, Truettner also considered which factors would increase the likelihood that engineers would use it in the field.
• Multi-use: The Fan Block-R performs multiple functions, reducing the amount of items engineers need to carry.
• Portable: Unlike a bulky piece of wood, the small size and strap make it easy for engineers to keep with them at all times.
• Durable: The Fan Block-R is made of ballistic nylon so it can’t easily be torn by sharp fan blades or general wear-and tear.
These benefits are reflected in the feedback Truettner hears from the field: “It’s easy to use. It’s easy to carry. It’s easy to put in place. It’s simple. And that’s key to getting someone to use something.”
Putting Innovation in Action with Leadership Support
Since Truettner created the Fan Block-R in 2019, ABM leadership has supported its production and promoted its use throughout the company. “The vice presidents and our upper leadership said, ‘We’ve got to do this.’ One thing I love about ABM is we want to keep our people safe, and ABM is not afraid to spend money on safety.”
At the local and regional level, senior managers and operations leaders are charged with ensuring that Fan Block-Rs are included with all lockout/tag out kits and thatABM engineers are trained on how to use it. Because of that support, Truettner’s “crazy idea” is now a widely used injury prevention tool. There hasn’t been a single injury related to fan blade or component motion at sites that use the Fan Block-R.
Making a Difference with a True Commitment to Safety
Truettner exemplifies ABM’s approach to safety. He understands that compliance is just a starting point. To keep people safe, sometimes you have to challenge the status quo. With employee-led innovations like the FanBlock-R, ABM is solving the common problems that lead to accidents. And that’s how we empower teams to put safety first.