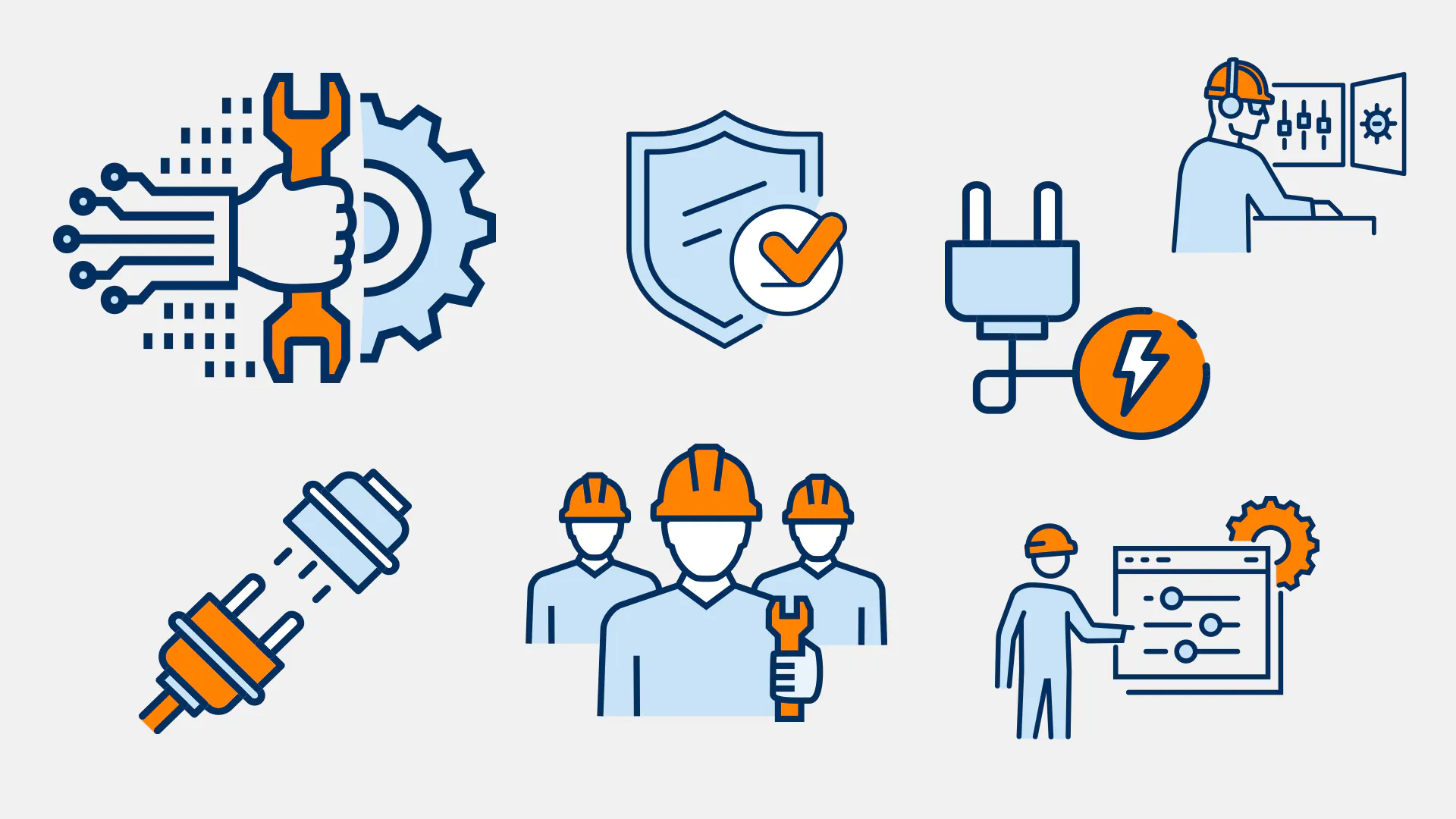
Uptime is everything. But without these best practices, downtime can bring your entire operation to an unexpected halt—and in some cases, threaten the safety of your employees and occupants. Ensure your electrical performance is only interrupted on your own terms. Regardless of industry, environment, or scale, dependable uptime is achievable by following electrical best practices like these.
1. Adopt Preventative Maintenance
One of the definitive ways to keep your equipment operating is to employ a preventative approach. While avoiding downtime can’t be guaranteed, a set schedule of maintenance will help keep your moments of downtime planned and minimal.
With a preventative maintenance plan, you can minimize failures through the regular inspection, cleaning, and replacement of your electrical assets. Potential hazards such as weak connections, failing insulation, and even dusty equipment can be addressed and remedied before your next cycle begins.1
2. Conduct Energized Testing
Sometimes detailed testing is needed to determine the condition of your electrical infrastructure. Working with a partner that is qualified in the use of advanced testing instruments can help identify electrical issues before they become serious problems. 2
If your infrastructure is due for an inspection but your facility can’t afford downtime, consider implementing energized testing. Energized testing can help technicians easily assess the condition of your electrical distribution assets without shutting your equipment down. It allows you to troubleshoot your assets while in operation, providing a diagnostic snapshot of the system conditions between your distribution assets and the downstream devices and production equipment they feed.2
3. Conduct Deenergized Testing
For a more extensive condition assessment, turn to deenergized testing: safer, more accurate method of system analysis conducted when your assets are turned off. Deenergized testing allows for superior diagnostic testing and a better overall assessment of the system conditions. Although this testing relies on planned downtime, allotting time for deenergized testing can decrease future chances of unexpected downtime by bringing otherwise hard-to-detect weaknesses to light.
With your equipment temporarily turned off, your infrastructure can be examined more carefully to measure contact and insulation resistance, dissipation factor/power factor, excitation, protection functionality, and more properties of the electrical circuit. These values can help identify areas of imminent failure. 2
4. Minimize Outdated Infrastructure
As businesses become more interconnected, everyday functions are increasingly reliant on computer and telecommunications systems. If your facility depends on a remote data center or maintains one in-house, make sure the capabilities of your infrastructure match your business requirements.
According to the American Society of Civil Engineers, the average cost of a data center outage is $8,851 per minute.3 Retiring decades-old infrastructure in and outside the data center can help your systems safely provide the speed your business needs. Ensuring cooling and backup power are operational can prevent overheating and additional downtime, as well.
5. Ensure Compliance
Risking the safety of your occupants in the name of uptime is never a smart practice. But when facilities cut corners and downplay the need for safe processes, they inadvertently put their own team members in harm’s way.
Following a national standard of safe electrical work practices like NFPA 70E can ensure facilities operate at a minimized level of risk. It can also support your uptime success by limiting the threat of arc flash, arc blast, and other hazards that lead to far more than just downtime. These dangers can cause severe injury, property damage, liability, and even death.4 Proactive prevention is crucial.
6. Observe Your Machinery
You don’t need testing instruments to notice major warning signs of equipment failure. Vibration, overheating, audible noises, and the like can indicate an asset on the verge of failure. While an active maintenance plan can help mitigate issues before they become noticeable, keeping your senses sharp regardless can hopefully prevent complete component failure, a situation that could lead to extended downtime. 4
7. Hire A Highly Qualified Team
When it comes to your facility’s electrical equipment, trusting the job to the right team is crucial. Letting unqualified or underqualified technicians maintain your infrastructure could be the difference between a safe, efficient environment and a downtime-riddled one.
You can trust that a certified team will have the knowledge and experience necessary to deliver high-quality electrical care. Look for certifications from a recognized agency such as NETA.5 With smarter insights, greater resources, and up-to-date training processes, a team of professionals can deliver the consistent uptime that your facility needs.
Ensure your facility is always as productive, efficient, and safe as possible—an experienced team of electrical professionals can help. ABM can provide the professional resources, the people, and the guidance to keep your facility’s electrical assets fully operational.
For more information about ABM’s Electrical Services, call 866.624.1520 to speak with our experts.
Sources
1. Electrical Preventative Maintenance Checklist
2. A look at the two principal motor testing methods: de-energized and energized
3. Electrical Infrastructure Report | ASCE's 2021 Infrastructure Report Card
4. NFPA 70E: Standard for Electrical Safety in the Workplace
5. Technician Certification - InterNational Electrical Testing Association